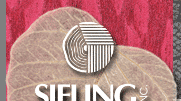 |
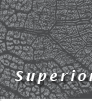 |
 |
 |
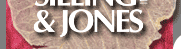 |
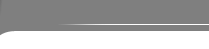         |
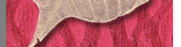 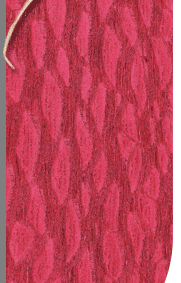 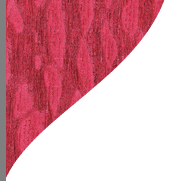 |
Three Types of Veneer Slicing Equipment
Rotary Lathe
Log is turned against a sharp blade and peeled off in one continuous or semi-continuous roll.
Slicing Machine
The flitch is raised and lowered against the blade and slices of the log are made.
Half Round Lathe
The log can be turned and moved in such away to expose the most interesting parts of the grain.
Each of these types of processes provides a very distinctive type of grain depending upon the species. When the veneer is sliced, a distortion of the grain occurs. The knife blade creates an open or "loose" side where the cells have been opened and a "tight' side.
The coloring differentiations created by the tight and loose side should not be confused with the "barber poling" effect. This takes place in certain wood where the same piece of wood appears to be dark or light depending upon which way it is viewed. Barber Poling is caused by polarization of the grain wherein the grain is slightly angled from the surface. The grain is either in shadow or penetrated by the light depending upon where the light source is coming from.
After slicing, veneer passes through a drying kiln, reducing the moisture content to approximately 8%. Bundles of veneer are made from sequences of veneer leaves, and generally include 24 to 32 leaves.
|
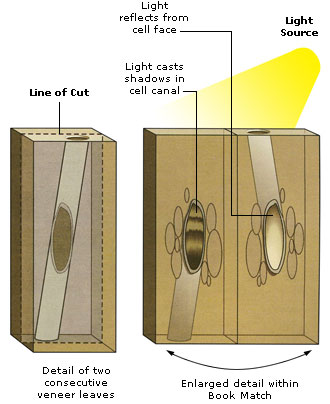
In the figure to the right the tight and loose sides are indicated by the way in which the piece of veneer bends or cups. |
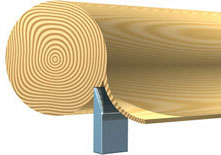
Rotary or lathe slicing produces wide sheets with a broad pattern and are difficult to match. This veneer is used primarily for economy or commercial grade applications.
|
Rotary Slicing
The whole log is mounted in a lathe and turned against the blade and guide, and is the most economical method of slicing. Rotary cutting (also rotary slicing or peeling) produces a continuous sheet of veneer as if the tree were a roll of paper being unrolled.
The veneer varies in pattern as the slices cut through the successive layers of growth rings, and no matching is possible for core grade and backing grade material. Birdseye, rotary ash and figured maple are rotary sliced, but sliced into sheets and sequenced much the same way as plain sliced veneer. The rotary slicing is an alternative to half round slicing in some species.
|
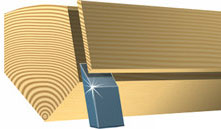
Rift cut (lathe) angle is 15° to minimize the ray flake effect in oak. Comb Grain is that portion which has very tight and straight grain.
|
Rift Slicing
By using a Staylog lathe that cuts with a rotary action, Rift slicing can avoid the appearance of flake. A quarter of the log is fixed to a plate, and the plate is then fixed acentric to the center line of a turning lathe. The flitch is rotated and comes in contact with the knife. The angle can be varied so that the wood is cut exactly to produce the very straight rift grain, generally found only in oak.
Though rift cut maple, walnut and cherry are often spoken of, these are actually the straighter grain portions of plain sliced or quarter sliced logs. Rift grain is generally the straightest, free from cathedrals and variations in grain, and is used to enhance verticality. It is also easily sequenced and matched.
|
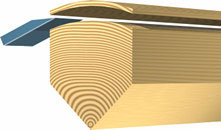
Half round slicing of wood is used to accentuate the variegated grain in burls and other specialty veneers.
|
Half-Round Slicing
The Half-Round slicing method consists of a half-round log attached to a face plate and turned around the lathe center. By increasing the radius of the cut, width is added to a narrow log through increasing the plane of the cut. Half round slicing of wood is used to accentuate the variegated grain in burls and other specialty veneers. It can also be used to achieve a flat sliced veneer appearance.
|
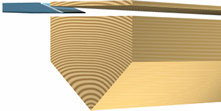
Plain sliced or flat sliced leaf width depends on log size and placement in flitch. Half round is a somewhat similar pattern achieved by turning a half log flitch on a lathe.
|
Plain Slicing (Flat Slicing)
Plain Slicing is used for all veneers that will not be rotary sliced. The veneer logs are sawn in half or into quarters to reveal the grain patterns inside the tree. A half-log (flitch) is mounted on a steel plate with the heart away from the blade and is then raised and lowered against the blade parallel to the center cut of the log.
Flat or plain slicing produces consecutive leaves of veneer. It’s considered the standard appearance of veneer (the "cathedral" or flame-shaped arch) that exemplifies plain sliced cherry, ash, oak and other species. These are ideally suited for wall panels and furniture because of the consistency in its grain and the ability to match sequences of leaves in book and end matches.
|
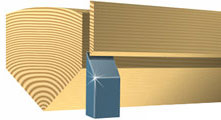
Flake pattern is produced when slicing through Medullary Rays in some wood species, principally oak. |
Quarter Slicing Veneer leafs that has very straight grain without the "flame" pattern is generally referred to as Quarter Sliced or Quartered veneer. A quarter log is mounted on a plate with the growth rings perpendicular to the plate, and the plate is raised and lowered against the blade in a direction radial to the center of the log. Because quartered leaves cut consecutively are narrower than plain sliced and typically contain straighter grain, larger diameter logs, usually from tropical species, are required.
Quartered white oak is often sliced specifically for its flake appearance, which is actually created by the veneer knife bisecting radial tubules in the tree structure, called medullary rays. Medullary rays are so small in most species as to be unnoticed in the grain pattern, but in the oak family they produce the distinct flake marking.
The ray flake should not be considered a defect, but rather a personal esthetic choice on the part of the designer. Quartered cherry, ash, maple, and red oak are usually the portions of a flat cut log where the heartwood is defective or is wide enough to be clipped and used as quarters. Quarter cut leaves can easily be sequenced and matched. |
|
|
|
|
Sieling and Jones, Inc. Terms and Conditions of Sales |
|